- Polypropylene spinning machine
- Polypropylene FDY equipment
- Polyester POY spinning machine
- Polyamide FDY common and high strength equipment
- Polyester FDY equipment
- Polyester high strength equipment
- polyester、Polyamide、 Polypropylene BCF equipment
- Small spinning machine
- All kinds of spinning special parts
- It turns out that the filament spun by the polypropylene FDY spinning machine has so many uses
- The national key and provincial key joint laboratories of the textile industry were launched in Shengze
- Textile News: AI and Intangible Cultural Heritage Dance Together: How Does Chinese Craftsmanship Amaze the World Stage?
- The 2025 Wuhan Shishang Industry Summit sets sail anew
- How does a polypropylene spinning machine reshape the quality genes of polypropylene filament?
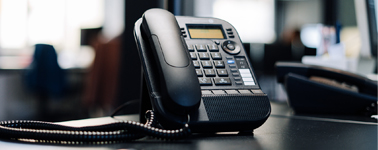
- Contact:Mr. Huang Guofu
- Cel:0086-13901505556
- Fax:0086-519-83341119
- Email:czfb5556@126.com
- Add:No. 288-8 ChangLi Rd, Huangli Town, Changzhou, JS PRV.
The spinning pump needs frequent maintenance and maintenance, so that all operations will not damage the accuracy of the parts, can not scratch the joint surface, can not oxidize and reduce the hardness. The replaced spinning pump must be cleaned by reusing the remaining melt, and the following five methods are used to remove the remaining melt.
Calcination
The calcining method, also called melting and burning method, is to heat the pump to 420-450°C in a special electric furnace to decompose the carbonized residue at high temperature.
The calciner can be disassembled or calcined as a whole. Dismantling can shorten the calcination time, especially for the overlap pump. Since the high thermal conductivity of molybdenum-containing high-speed steel is small, the heating rate of the electric furnace during calcination cannot be higher than 100°C/h, and the temperature in the furnace must not be strictly controlled to exceed 450°C. Otherwise, the high temperature will cause the hardness of the pump to drop or cause deformation. Destroy the accuracy of the pump.
The disadvantage of this method is that the heating is not uniform enough and the operating conditions are poor.
Salt bath method
The pump changed on the spinning machine was disassembled, placed in a hanging basket and hung in a salt bath to clean it.
There are two types of salt bath: one is a two-component salt bath of sodium nitrite and sodium nitrate with a ratio of 1:1, and the other is potassium nitrate, sodium nitrate and nitrous acid with a ratio of 53:7:40. Sodium salt three-component salt bath. At 300-400 °C, salt bath treatment 1-2h, the parts of the pump can be cleaned. The advantages of this method
The point is that the temperature is easy to control evenly, and the pump in the salt bath is isolated from the air, making the surface less susceptible to oxidation.
However, the salt bath consumption of this method is large, the effect is reduced with a long time, and there is a certain degree of corrosion.
Triethylene glycol method
The pump was immersed in a triethylene glycol bath and heated to 260°C for washing. Due to the reaction of triethylene glycol with polyester, it was dissolved or swollen and removed.
The components processed by this method can play a role in protecting accuracy and smoothness, but the processing time is longer than 24 hours.
Fluidized bed method
Put a certain number of meshes of Al2O3 powder into a fluidized bed and heat it up to 300°C. Disassemble the pump, place it in a hanging basket and hang it in a fluidized bed. The fluidized bed throws high-temperature Al2O3 powder on the pump's parts to make the pump The polymer undergoes an oxidation reaction.
Compared with the calcination method, this method increases the heat transfer medium, shortens the processing time and lowers the processing temperature.
Vacuum calcination
Calcining in a vacuum system can reduce the processing temperature and accelerate the reaction. After the above method is processed, ultrasonic cleaning can be used again.
Each method has its own advantages, but there are also certain limitations. The actual operation should be based on the existing material conditions, select the appropriate cleaning method.
Changzhou Fubon Chemical Fiber Machinery Factory mainly produces Polyester POY spinning machine, Polypropylene FDY Spinning Machine, FDY Spinning Machine, Polyester FDY Spinning Machine, Polypropylene spinning machine, Polyester POY spinning machine, Nylon FDY Spinning Machine, Spandex Spinning Machine, Spandex Equipment, Spinning Parts, Dacron Small Testing Machine, PP Small Testing Machine, Polyester POY spinning machine.
- The national key and provincial key joint laboratories of the textile industry were launch
- It turns out that the filament spun by the polypropylene FDY spinning machine has so many
- Textile News: AI and Intangible Cultural Heritage Dance Together: How Does Chinese Craftsm
- The 2025 Wuhan Shishang Industry Summit sets sail anew
- How does a polypropylene spinning machine reshape the quality genes of polypropylene filam
- How to scientifically evaluate the working efficiency of a polypropylene spinning machine
- The Battle Song of Longcheng | Beyond Victory and Defeat, the spirit of Changzhou burns Fo
- @All partners: The Summer Solstice has arrived. Fubang Machinery takes you to unlock the S
- The 2025 Greater Bay Area International Textile Yarn Expo was held
- Detailed Explanation of the Inspection Standards for Polypropylene Spinning Machine Equipm