- Polypropylene spinning machine
- Polypropylene FDY equipment
- Polyester POY spinning machine
- Polyamide FDY common and high strength equipment
- Polyester FDY equipment
- Polyester high strength equipment
- polyester、Polyamide、 Polypropylene BCF equipment
- Small spinning machine
- All kinds of spinning special parts
- How does a polypropylene spinning machine reshape the quality genes of polypropylene filament?
- The 2025 Wuhan Shishang Industry Summit sets sail anew
- How to scientifically evaluate the working efficiency of a polypropylene spinning machine
- The Battle Song of Longcheng | Beyond Victory and Defeat, the spirit of Changzhou burns Forever! Fubang Chemical Fiber Machinery is cheering for the Changzhou team of the Scottish Premier League!
- @All partners: The Summer Solstice has arrived. Fubang Machinery takes you to unlock the Summer Solstice health guide and start a healthy summer!
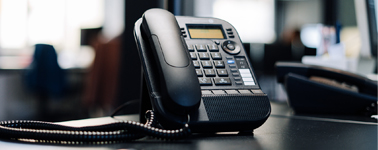
- Contact:Mr. Huang Guofu
- Cel:0086-13901505556
- Fax:0086-519-83341119
- Email:czfb5556@126.com
- Add:No. 288-8 ChangLi Rd, Huangli Town, Changzhou, JS PRV.
Always feel that the cost of operations has been rising, but it is difficult to find where the cost of "position", we call it "implied." The following lists the nine hidden costs that may exist in the textile enterprises. Can textile companies use this self-check to see if you are "invisible"?
1.TALENT FLOW COST Talent Flow Cost
There are many factories that are lacking in human resources management. They think that the talented people are unlimited and become "iron-plated camps." Naturally, employees have become the "arms of the water."
It must be said that the departure of technicians is a big cost to the company. Because the company has to bear the up-front costs of recruiting new employees in this position, it also has to take on the risk that new employees will be suitable for the position. New employees also need to go through the run-in period to adapt to the factory's process.
The departure of an important employee may result in the loss of important internal data or information. After he leaves the company, he is likely to enter his own competitor's company.
Therefore, the loss of employees, especially old employees, will undoubtedly bring the company several times more than its income. After many small factories have been in business for many years, you find that they have always been such a small team, and no one other than the boss has stayed from the beginning of the establishment of the company. I think this may be an important reason why it cannot develop.
2, OVERTIME COST overtime cost
Many employers always believe that employees' “overtime work” after work is “overtime” is a kind of professionalism. As everyone knows, this may imply high costs for three reasons:
First, the reason for overtime is not necessarily because the task is too heavy, but because the work efficiency of employees is low. Overtime means low efficiency. If the objective task is really heavy, then the company should replenish new personnel and positions in time to be truly development and progress.
Secondly, overtime requires more staff energy and physical strength, and seriously overstretch the health of employees. In the long run, some important employees will not be able to exert their performance for a long time, and there will be hidden risks for the company. For example, some mechanical operators Long hours of overtime lead to mental disorders and accidents, and companies have to pay a heavy price for this.
Thirdly, overtime employees are not necessarily “respectful to work”. Some employees are known as overtime when they are off work. They use the company’s resources to engage in their personal affairs. They also receive the company’s overtime pay. Many companies lose important data and lose data. All of this happened during off hours, and overtime became a corner of the company's "filth."
3, PROCESS COST manufacturing process costs
The chaos in factories is too much because of processes. This is a common problem in business management. For slow-moving companies, the process must be confusing or unreasonable. They have to bear high costs for this, but they have always ignored them.
The process is the industrial chain in which the company operates. Like the assembly line, there is no scientific and rational manufacturing process. It also loses systematic control over all processes. Many jobs are abandoned halfway, and many jobs need to be reworked. But have to admit that this will become a mess that wraps the factory forward.
4, CONFERENCE COST meeting costs
The operation of the factory is nothing more than a race against time. The meeting is a collective activity of the factory to solve problems and issue directives, but it is also a high-cost business activity.
Because this activity is often a group activity in which many leaders participate. Every minute means the total number of minutes of attendees, and many companies’ managers do not have the skills to hold meetings. “There is no preparation before the meeting. No theme, no implementation after the meeting, no need for participation, no time control, and no phenomenon of speech.
5, POSITION DISLOCATION COST Post misplaced costs
In human resources management there is a famous saying "put the right people in the right place."
Some factories arrange technicians to spend a lot of time every day to mop the floor, clean the sanitation, and dye the tank setting machine. Some leaders also take the lead to participate in it. It looks like a good thing. People can not help but sigh, this factory is engaged in printing and dyeing, how could spend so high wages, please come to an unprofessional cleaner.
In fact, this shows that the bosses have a very clear mentality. They think that the recruitment of these employees is to use them. If they can do it by themselves, they do not need to spend more money. However, we found that they paid a high price.
6, PURCHASING COST purchase costs
Purchasing has different ways in different companies, but this is an important part of the costs that affect the operation of the factory. We often only focus this cost on the price and quantity of procurement and it is difficult to see other factors besides.
Once there was a branch of a printing and dyeing company, when it was doing a new project, the daily operating cost was 80,000 yuan. However, on the eve of its listing, the procurement department spent a week in order to purchase more than 100,000 yuan in supplies. It is to find low-cost suppliers to save purchase costs. The entire marketing team therefore waited more than a week to sign the contract with the customer.
This phenomenon actually exists in many companies. The blind pursuit of reducing the direct cost of procurement and ignoring the simultaneous existence of "invisible costs." Of course, there is no conflict between reducing the direct cost of procurement and this article. Here, we must say that the procurement department of an enterprise must comprehensively balance the various indicators from the perspective of overall operations in order to truly control the cost of procurement.
7, COMMUNICATION COST communication costs
In today's economically turbulent environment, the operating pace of textile companies has also become increasingly fast. However, everything has a certain limit. The fast-paced operation has brought many troubles to enterprises.
Communication is an important part of the company's operations. Many companies are doing a lot of system training and spiritual training, but most of them don't have "communication skills" training.
In most factories, you will find that in the process of communication between colleagues, there will be serious distortions, or words inadvertently, or unanswered questions, or hundreds of people ... this phenomenon, that small, so many processes Become an invalid process or lose a lot of important opportunities. If you say something big, it may cause hidden trouble for the company. This is a typical cost increase due to poor communication.
8. STAGNANT RESOURCE COST stagnant resource costs
This is the most widespread "implied form", such as idle equipment, backlogs of inventory, low-utilization job occupations, idle funds, and shelved businesses. Therefore, the number of stagnant resources in an enterprise reflects the level of utilization of enterprise resources.
9, CORPORATE CULTURE COST corporate culture costs
Some people say that corporate culture is like the soul of a company and it is reflected in the spiritual outlook of each of its members. This culture was established at the initial stage of the establishment of the company. He was influenced by the company's founders' culture, habits, skills, occupations, likes and dislikes, and it was therefore said that corporate culture is the boss culture.
But to say that corporate culture will become a cost, perhaps many people disagree, but it is. We will find that the employees of some textile companies are apathetic and extremely inefficient in doing things. No matter how excellent the employees are, as long as they enter, they will soon leave or they will become so. We cannot but say that this is an “environmental” issue. And this "environment" is exactly the corporate culture of this company.
Corporate culture is like the life of a business. It can be accompanied by the life of a business. It can only be adjusted and cannot be rebuilt.
The details determine the success or failure. In the textile industry, as long as the bosses take the cost of each link, it is believed that the competitiveness of the company will naturally converge.
Changzhou Fubang Chemical Fiber Machinery Factory mainly produces: polyester industrial yarn spinning combined machine, polyester POY spinning machine, polypropylene FDY spinning machine, polypropylene FDY production line, polypropylene FDY equipment, polypropylene FDY machinery, polyester industrial yarn spinning combined machine, Polyester FDY spinning machine, polypropylene spinning machine, polyester FDY production line, polyester FDY machine, nylon FDY spinning machine, polyester industrial yarn spinning machine.
- The 2025 Wuhan Shishang Industry Summit sets sail anew
- How does a polypropylene spinning machine reshape the quality genes of polypropylene filam
- How to scientifically evaluate the working efficiency of a polypropylene spinning machine
- The Battle Song of Longcheng | Beyond Victory and Defeat, the spirit of Changzhou burns Fo
- @All partners: The Summer Solstice has arrived. Fubang Machinery takes you to unlock the S
- The 2025 Greater Bay Area International Textile Yarn Expo was held
- Detailed Explanation of the Inspection Standards for Polypropylene Spinning Machine Equipm
- Small samples of Changshu home textiles have driven large orders
- Entering the Polypropylene Spinning Machine: A Grand Revelation of the Four Functional Zon
- Textile News | Over 40 embroidery styles compete on the same stage, Summer Cloth embroider